PRIMUS GROUP, INC. — Facilitating Trade for Importers, Big or Small
August 25, 2021 | 5 min to read


Sponsored Content
U.S. importers, especially small to midsize companies, are feeling the heat as enforcement of FSMA’s Foreign Supplier Verification Program (FSVP) hits home. FSVP shifted food safety responsibility and liability from all entities within the supply chain to the importer, making FDA’s importer-of-record list more important than ever.
“Importers today are responsible for verifying that the risks have been identified, preventive controls have been put into place, the preventive controls have been validated or proven effective, and that the entire system is being monitored to verify continued effectiveness. The big change, in short, is that the importer is now responsible for FSVP compliance;’ says Cynthia Temblador, Azzule Core Support’s FSVP Program Director.
These requirements can be complex, costly, and overwhelming, behooving impacted companies to enlist specialized expertise and ongoing, coordinated strategies to allay risks and gain competitive advantage. Importers today must consider whether to internalize FSVP efforts, to outsource them, or to use a hybridized approach.
“The key is helping importers to optimize ways they can fit their business into FDA’s expectations of them and find their niche by either expanding or maybe being more selective in what they’re importing;’ adds Joseph Myers, Communications and Training Specialist at Primus Group.
“The FDA was first going to the largest companies, working its way down, and now it is making contact with importers that are in some cases really small operations, and a number of warning letters have gone out;’ says Myers. “We know of instances where people not on FDA’s list of importers of record got letters from FDA saying they were in violation of he Foreign Supplier Verification Program. We have clients who are concerned they’re going to get into some kind of trouble and need some direction:’
“Some of these importers are really struggling to find the right way to comply with FSMA and FSVP and have already been visited by the FDA;’ says Rebeca Perez, Chief Ag Strategist at Azzule. Azzule’s Core Support was formed in November 2019 to address the challenges confronting many small to mid-size importers burdened by the ramped-up demands of FSVP.
While larger shipper entities are more equipped to navigate the FSMA rules, Azzule saw a significant gap that needed to be filled (and in some respects, to help even the playing field). Azzule offers a multi-faceted, fully integrated platform for those lacking the necessary resources, skilled personnel, or specialized know-how to maneuver through the compliance hoops of a fragmented global supply chain. Azzule and its Core Support Services, in partnership with PrimusLabs, is uniquely designed to expedite safe and integrated border trade which is paramount to survival in fresh produce.
“When it comes to FSVP compliance, importers are experiencing emerging challenges with foreign suppliers;’ says Temblador. “They need to educate the supplier on what’s involved, the reasons for the FDA regulation and the advantages to implement that system, etc. It’s overwhelming for some importers, and we’re trying to help them with our services and training to establish that connection:’
Core Support provides compliance assistance directly to importers of record, and Temblador can serve as a qualified individual for a company if it doesn’t have one. Even large importers may still require Core Support services, not because they don’t have a food safety director, but because they may have thousands of foreign suppliers, and the clerical work of keeping track of all those suppliers and all the documents and audit records is a big job.
On the other hand, according to Myers, “There are the really small importers, the mom and pop operations, that don’t have a food safety person on staff, and they’re intimidated by this idea of being responsible for the food safety of a supplier who might be thousands of miles away and may not speak the same language, etc. Temblador and her colleagues can help them navigate their suppliers, get the information required of them, and make sure all of FDA’s requirements are met;’ he explains.
“There’s a lot at stake;’ says Perez. In addition to the FDA requirements, evaluating various country regulations and procedures adds another complication.
“Buying tomatoes from Canada, for example, is not the same thing as buying tomatoes from Mexio;’ she says. “Also, retailers have their own sets of performance standards for compliance:’ She explains, noting, ” … because we’ve been working in this business for a long time and have extensive food safety experience, we understand what is required to comply with each buyer’s expectations and at the same time with the FDA requirements’.’
To simplify the complexities, Azzule developed a compliance grid software platform – the Azzule Supply Chain Program – in which the buyer can set up new requirements and then the connected suppliers in that system know which tasks they must accomplish to satisfy that particular buyer. “It’s about moving information all the way through the supply chain from the farm level up to the largest and most sophisticated buying entities in the world;’ says Myers.
Myers continues, “Primus Group aims to take a comprehensive approach to food safety, and addressing different company needs across a wide range of service areas, flowing information directly into the supply chain … to help people do business and to grease the skids of international commerce.”
Brought to you by Primus Group Inc. 805-922-0055
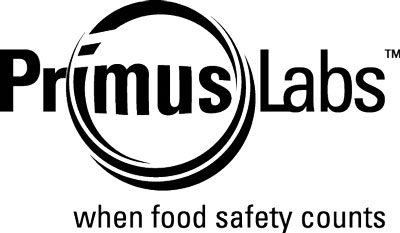
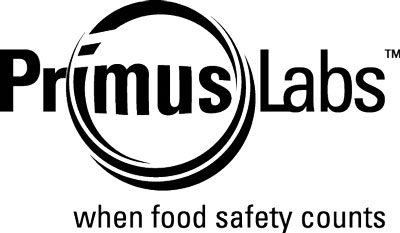
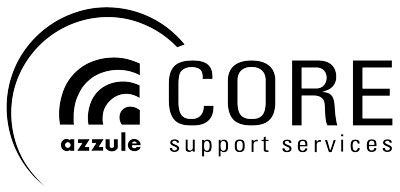
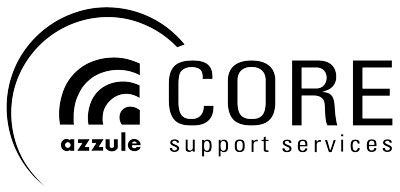
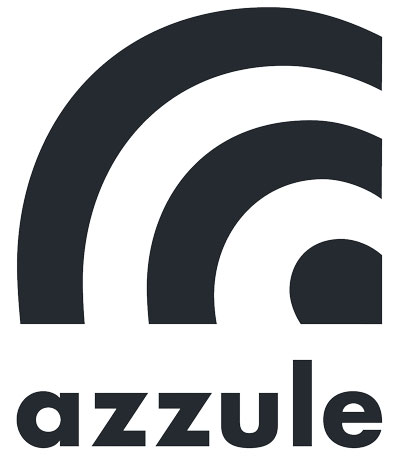
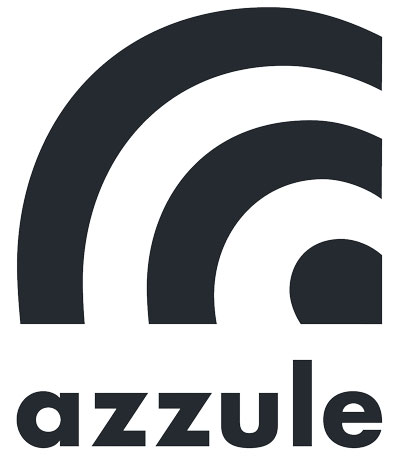
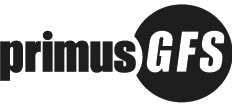
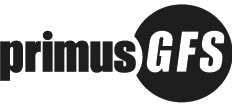
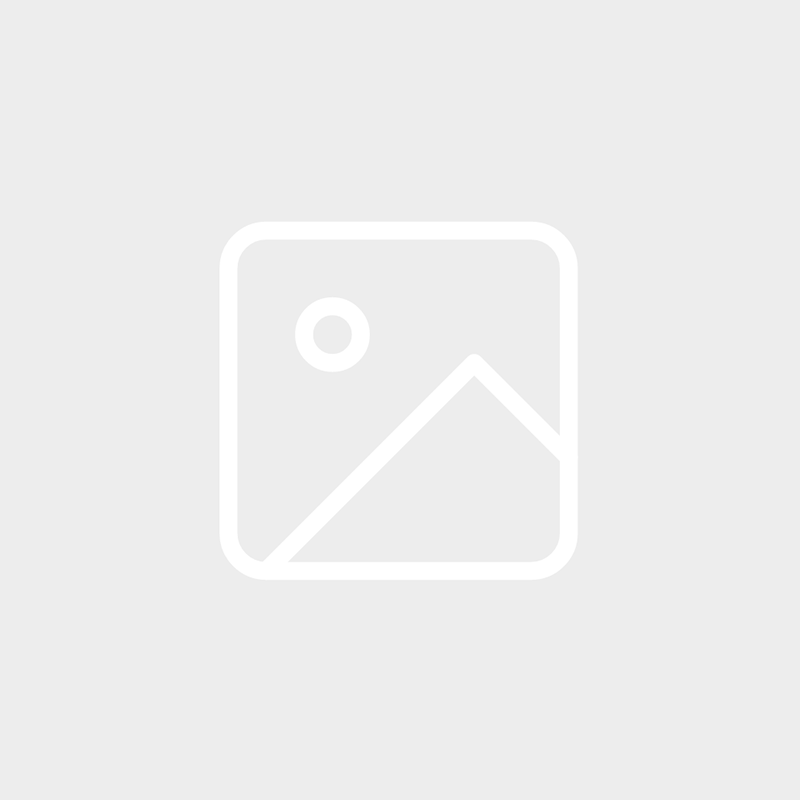
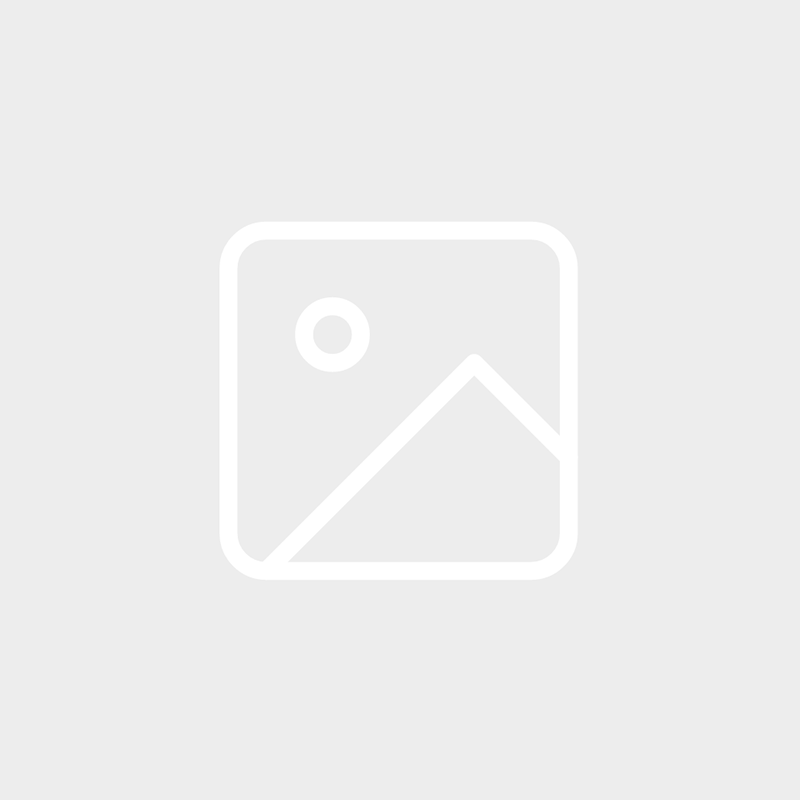
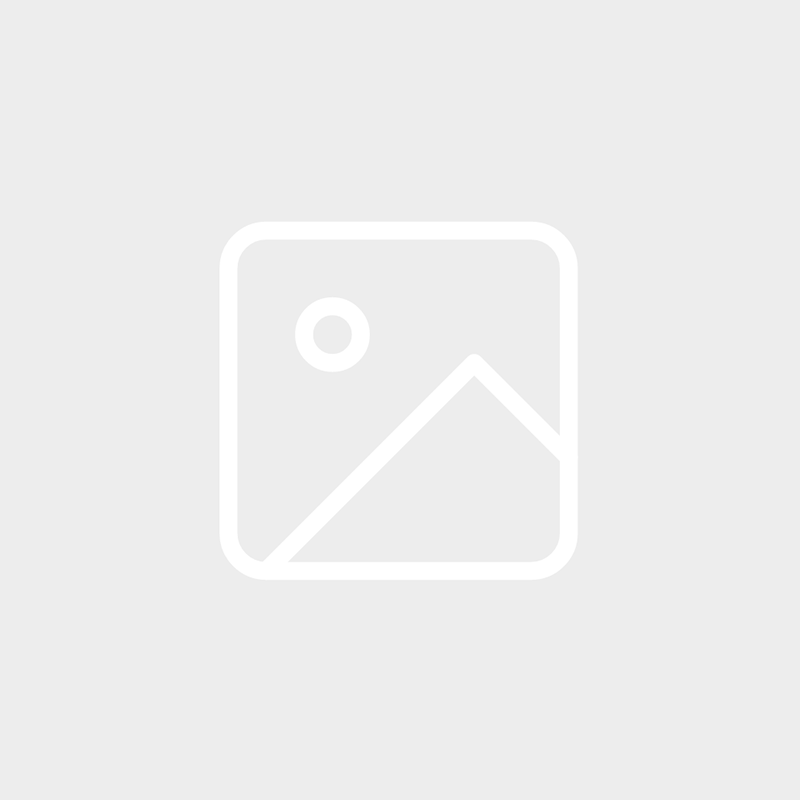
Primus Labs
Contacts
Address
Av. Del Carmen #250 Interior 34 Parque Industrial Grunpark La Llave 1 Sur. Parques de Santa Cruz del Valle 45618 Tlaquepaque, Jalisco
Phone
332 464 6028Website
https://www.primuslabs.com/