Inline Plastics – First USA Manufacturer to Infuse All Products with Post Consumer Content Derived from Advanced Recycling
June 17, 2021 | 4 min to read
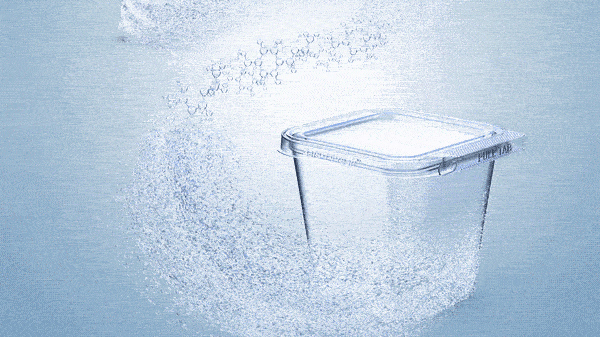
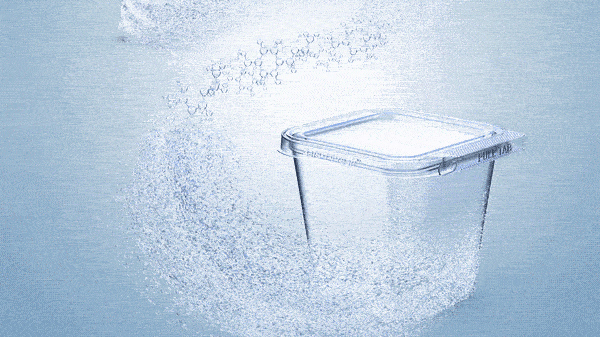
Sponsored Content
Originally printed in the May 2021 issue of Produce Business.
Shoppers increasingly want to buy their fresh fruits and vegetables in some type of packaging. In fact, the U.S. demand for produce packaging is projected to increase 4% annually, according the May 2018-released report, Produce Packaging Market in the U.S., by the Cleveland, OH-headquartered, The Freedonia Group. Yet, at the same time, another survey showed over half (55%) of all consumers surveyed at least occasionally made food and beverage selections “with sustainability in mind”. This insight is based on a report titled, Sustainability 2019: Beyond Business as Usual, which was published by the Bellevue, WA-based The Hartman Group.
Now, Inline Plastics offers a best of both world’s solution. That is, high-performing packaging that protects and presents fresh produce at its best while offering the lowest carbon footprint on the market.
A Commitment to Sustainability and Product Innovation
In 2020, Inline Plastics announced its revolutionary integration of a new material called rDPET™ throughout all their products under the Safe-T-Fresh and Essentials brands. This makes the Shelton, CT headquartered PET packaging manufacturer the first in the U.S. to develop food grade material infused with post-consumer or recycled content.
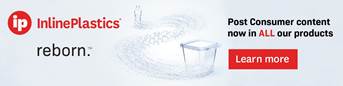
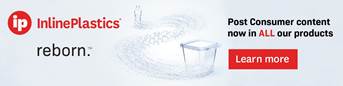
This milestone achievement was bringing this new technology and proprietary process to market. The crux of what differentiates ‘reborn’ or rDPET™ from traditional PET plastic is that the process takes recycled PET and breaks it down into its original building blocks or polymers. Then, these are combined with fresh or virgin ones.
Since everything happens at the molecular level, the end-product rDPET packaging retains all the strength and clarity of clean new plastic. What’s more, Inline Plastics further reduced negative environmental impacts by powering its thermoforming production in-part by using solar panels.
By using rDPET™, coupled with an energy efficient proprietary manufacturing ‘direct to sheet’ process, Inline Plastics realizes the following environmental benefits in comparison to traditional PET:
* Diverts nearly 1 billion water bottles from the world’s oceans and landfills annually
* Uses over 50% less energy during material production
* Reducing the carbon footprint by 112,000 acres of forest or emissions equal to 233 million miles driven per year
Benefits to Inline Plastic’s customers – growers, food processors and retailers and their customers – is similarly strategic. Specifically, more companies are building their portfolio with 5- to 10-year sustainability goals in mind. By applying 10% post-consumer content to all Inline Plastics products, customers can take advantage of the recycled content for their sustainability efforts without being restricted to a specific product line. The company can supply customers annual Environmental Contribution Certificates showing CO2 savings that resulted from purchasing Inline products made from the very low carbon footprint rDPET™, which can then be shared with their consumers.
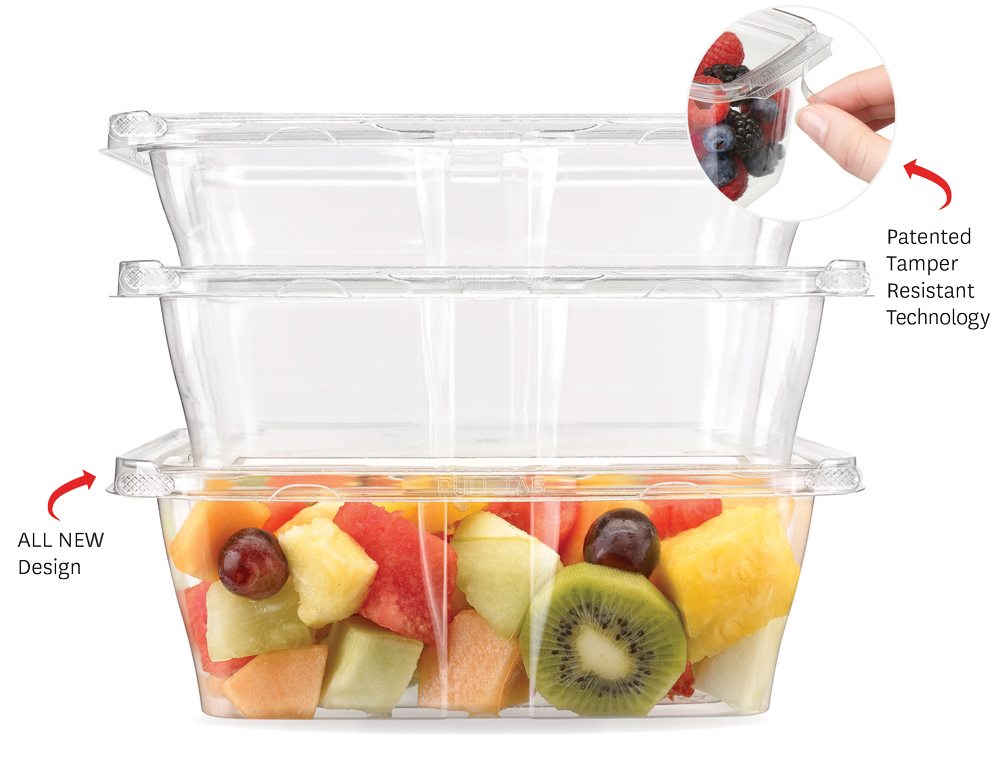
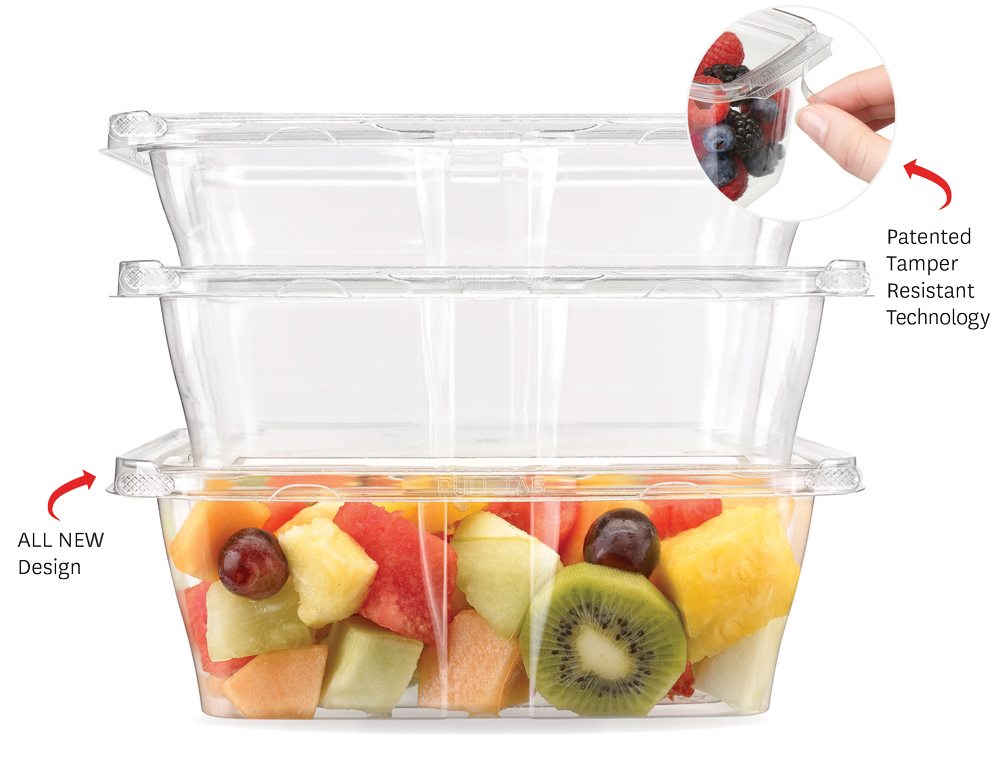
The integration of rDPET™ across all Inline Plastics product lines was no small task. However, the company knew the importance of this solution to its customers. Plus, the old ways just weren’t the best anymore. Case in point is that traditional mechanical recycling reduces material performance, impacts visual clarity, and impacts the merchandising of the product. Leveraging advanced recycling technology required a couple of years of fine tuning before the Inline was satisfied in bringing this process and its products to the market.
The work isn’t done yet. One of the big challenges is that there is a high demand and limited supply of post-consumer content. Globally, recycling rates today are around 9 percent. This year, the company is ramping up to 10 percent post-consumer content, with the goal of increasing this percent as supply becomes more available. To this end, Inline Plastics is working with sustainability organizations to improve recycling rates in the U.S. This forward thinking work plus the use of chemical recycling enables plastic to be reused and avoid landfills or even worse, make its way into the world’s oceans.
Something for Virtually Every Fresh Fruit & Vegetable
Inline Plastics is no stranger to innovation. In 2006, the company created the first tamper evident and tamper resistant technology in the market with its Safe-T-Fresh®. Starting in 2008, Inline transitioned from OPS to an energy efficient, environmentally friendly PET called DPET. Compared to OPS the environmental impact of DPET is more favorable and sustainable, in comparison, and it is 100% curbside recyclable.
Today, the company offers over 300 products in 15 product families over the two brands, Safe-T-Fresh and Essentials. Given the unparalleled leak resistance, all 7 Safe-T-Fresh® families are a great choice for fruit and vegetables. Available Safe-T-Fresh products range from 2oz to 128 oz with many different shapes and sizes to fit almost every application.
Over the last 4 years, Inline Plastics has launched 6 major new product families – SquareWare®, RoundWare®, SnackWare®, PagodaWare®, Snackers, Microwaveables, as well as refreshed their popular 20-64 oz rectangles – which are all very applicable for fruit and vegetable packaging.